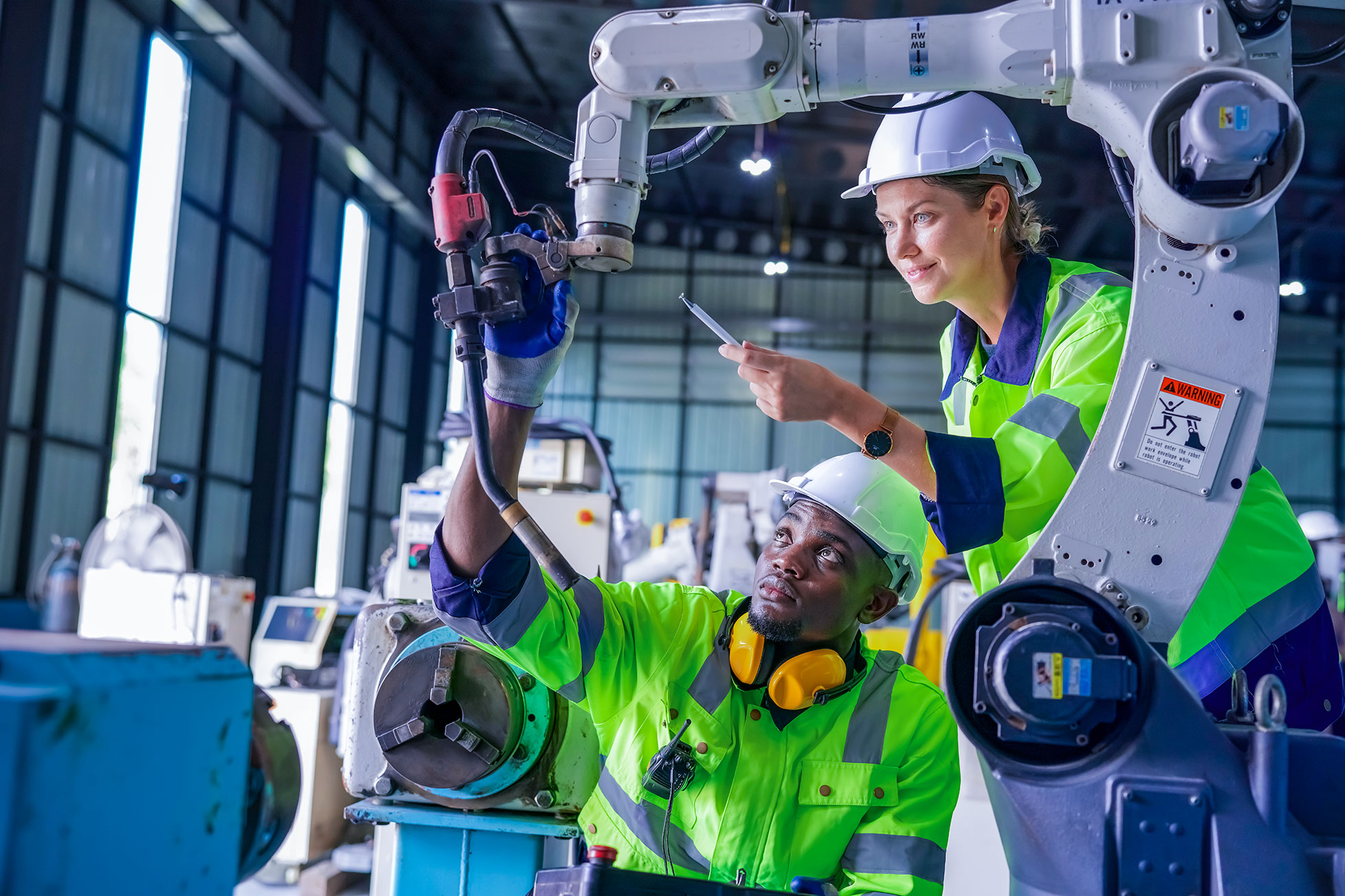
A Quarta Revolução Industrial, também conhecida como Indústria 4.0, está transformando radicalmente o cenário da manutenção industrial no Brasil. Esta nova era tecnológica, caracterizada pela fusão de tecnologias digitais, físicas e biológicas, traz consigo uma abordagem revolucionária para a gestão e manutenção de ativos industriais: a Manutenção Preditiva.
A manutenção preditiva, potencializada pelas tecnologias da Indústria 4.0, permite às empresas prever falhas em equipamentos antes que elas ocorram, otimizando processos, reduzindo custos e aumentando a eficiência operacional. Neste artigo, exploraremos como essa sinergia está moldando o futuro da indústria brasileira.
Tecnologias IoT na Manutenção Preditiva
No coração da revolução da manutenção preditiva está a Internet das Coisas (IoT). Sensores inteligentes, instalados em máquinas e equipamentos, coletam dados continuamente sobre seu desempenho, temperatura, vibração e outros parâmetros críticos. Esses dados são transmitidos em tempo real para sistemas centralizados, onde são analisados para identificar padrões e anomalias.
A implementação dessas tecnologias tem mostrado resultados impressionantes. Segundo um estudo recente da ABIMAQ (Associação Brasileira da Indústria de Máquinas e Equipamentos), empresas que implementaram IoT na manutenção viram uma redução média de 30% nos custos de manutenção. Esta economia significativa é apenas um dos muitos benefícios que a IoT traz para o setor.
Análise de Dados e Inteligência Artificial
A verdadeira potência da manutenção preditiva vem da análise avançada dos dados coletados. Técnicas de Machine Learning e Inteligência Artificial são aplicadas para processar enormes volumes de dados (Big Data) e extrair insights valiosos. Esses algoritmos podem identificar padrões sutis que precedem falhas, permitindo intervenções precisas e oportunas.
O interesse das indústrias brasileiras nessa tecnologia é evidente. Uma pesquisa recente da PwC Brasil revelou que 65% das indústrias no país planejam investir em análise avançada de dados nos próximos dois anos. Este dado demonstra claramente a crescente conscientização sobre a importância dessa tecnologia para manter a competitividade no mercado global.
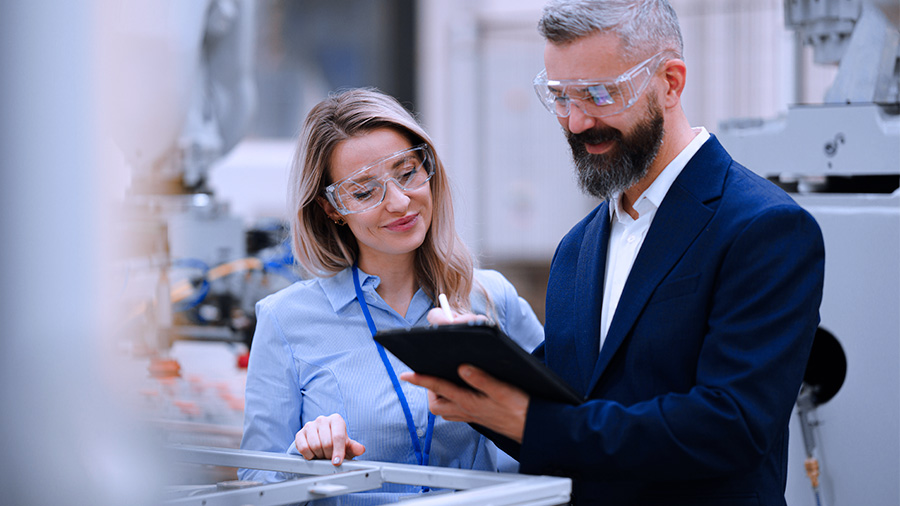
Benefícios da Manutenção Preditiva
A adoção da manutenção preditiva traz uma série de benefícios tangíveis para as indústrias:
- Redução de paradas não programadas: Ao prever falhas com antecedência, as empresas podem planejar manutenções em momentos oportunos, minimizando interrupções na produção.
- Aumento da vida útil dos equipamentos: Intervenções precisas e no momento certo prolongam a vida operacional das máquinas.
- Otimização de custos: Redução de gastos com peças de reposição e mão de obra para reparos emergenciais.
- Melhoria na qualidade e produtividade: Equipamentos bem mantidos produzem com mais qualidade e eficiência.
Um relatório da FIESC (Federação das Indústrias de Santa Catarina) corrobora esses benefícios, mostrando que indústrias que adotaram manutenção preditiva tiveram um aumento médio de 25% na disponibilidade de equipamentos. Este aumento na disponibilidade se traduz diretamente em maior produtividade e competitividade.
Implementação de Sistemas de Monitoramento em Tempo Real
A implementação de sistemas de monitoramento em tempo real é um passo crucial para a manutenção preditiva. Este processo envolve várias etapas:
- Avaliação inicial: Identificar equipamentos críticos e definir parâmetros a serem monitorados.
- Seleção de tecnologia: Escolher sensores e sistemas de coleta de dados apropriados.
- Instalação e integração: Implementar a infraestrutura física e digital necessária.
- Treinamento: Capacitar a equipe para operar e interpretar os novos sistemas.
- Ajuste e otimização: Refinar continuamente o sistema com base nos resultados obtidos.
Um dos maiores desafios na implementação é a integração com sistemas legados. Muitas indústrias brasileiras ainda operam com equipamentos mais antigos, que não foram projetados para conectividade digital. Soluções de retrofit e o uso de gateways IoT podem ajudar a superar esse obstáculo, permitindo que mesmo máquinas mais antigas sejam incorporadas ao sistema de monitoramento.
Casos de Sucesso no Brasil
Várias empresas brasileiras já estão colhendo os frutos da manutenção preditiva. Um exemplo notável é a Petrobras, que implementou um sistema de Inteligência Artificial para prever falhas em suas plataformas de petróleo. Este sistema reduziu o tempo de inatividade em 40%, resultando em economias significativas e aumento da produtividade.
Outro caso de sucesso vem de uma grande indústria siderúrgica brasileira (cujo nome foi mantido em sigilo por questões de confidencialidade). A empresa implementou sensores IoT em seus altos-fornos e laminadores, resultando em uma economia anual de R$ 5 milhões em custos de manutenção. Além disso, a empresa relatou uma redução de 60% nas paradas não programadas.
Como será o Perfil do Profissional para Atuar na Indústria 4.0?
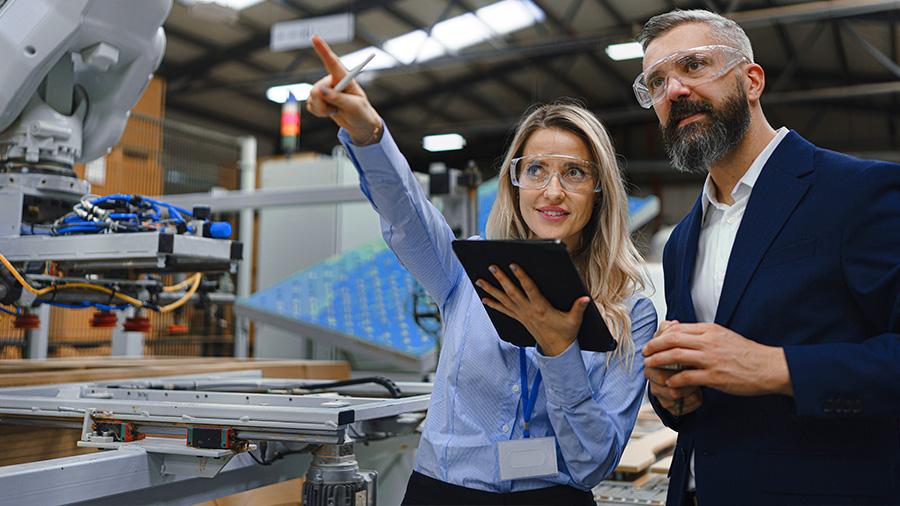
A transição para a Indústria 4.0 demanda um novo perfil de profissional, capaz de lidar com as complexidades das novas tecnologias. O profissional ideal para atuar neste cenário deve possuir:
- Habilidades técnicas: Conhecimentos sólidos em análise de dados, programação e IoT são essenciais. Familiaridade com linguagens como Python e R, bem como com plataformas de análise de dados, é altamente valorizada.
- Soft skills: Adaptabilidade, pensamento crítico e capacidade de aprendizagem contínua são cruciais em um ambiente em constante evolução.
- Formação interdisciplinar: Uma base em engenharia, complementada por conhecimentos em TI e ciência de dados, forma o perfil ideal para navegar na interseção entre o mundo físico e digital da Indústria 4.0.
A demanda por esses profissionais é alta, e a oferta ainda é limitada. Uma pesquisa recente da CNI (Confederação Nacional da Indústria) revelou que 72% das empresas industriais brasileiras têm dificuldade em encontrar profissionais qualificados para atuar com tecnologias da Indústria 4.0. Este dado ressalta a necessidade urgente de programas de capacitação e atualização profissional no setor.
Desafios e Perspectivas Futuras
Apesar dos avanços, a indústria brasileira ainda enfrenta desafios na adoção plena da manutenção preditiva e das tecnologias da Indústria 4.0:
- Investimento em infraestrutura digital: Muitas empresas ainda precisam modernizar sua infraestrutura de TI para suportar as demandas de conectividade e processamento de dados da Indústria 4.0.
- Cibersegurança: Com o aumento da conectividade, cresce também a vulnerabilidade a ataques cibernéticos. Investimentos em segurança da informação são cruciais.
- Regulamentação: O marco legal para questões como propriedade e compartilhamento de dados industriais ainda está em desenvolvimento no Brasil.
Olhando para o futuro, tecnologias emergentes como gêmeos digitais e realidade aumentada prometem levar a manutenção preditiva a um novo patamar. Gêmeos digitais – réplicas virtuais de equipamentos físicos – permitirão simulações ainda mais precisas e testes de cenários sem riscos. Já a realidade aumentada poderá auxiliar técnicos em campo, fornecendo informações em tempo real durante as operações de manutenção.
Qual a real importância destas tecnologias para as indústrias no Brasil?
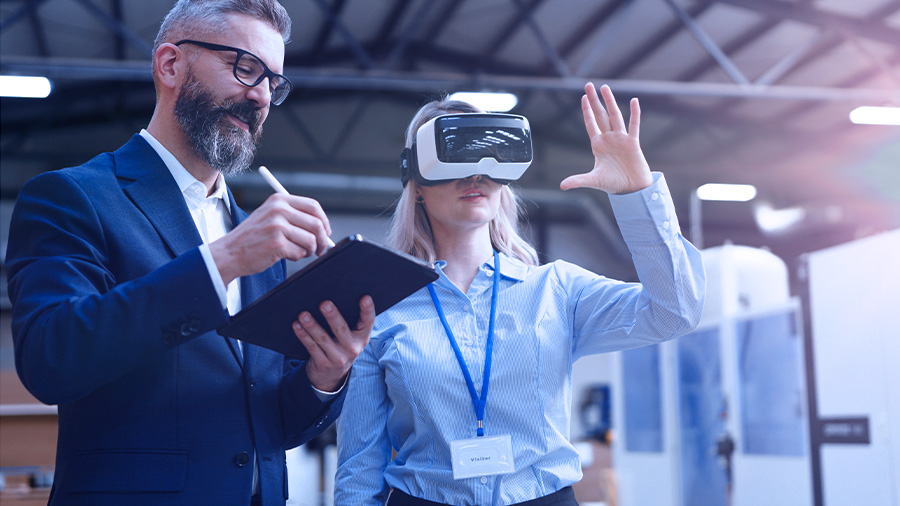
A manutenção preditiva, impulsionada pelas tecnologias da Indústria 4.0, está revolucionando o setor industrial brasileiro. Ao permitir a antecipação de falhas, otimização de processos e redução de custos, essa abordagem inovadora está se tornando não apenas uma vantagem competitiva, mas uma necessidade para as empresas que desejam se manter relevantes no cenário global.
Os benefícios são claros e mensuráveis: redução significativa nos custos de manutenção, aumento da disponibilidade de equipamentos e melhoria na eficiência operacional. Casos de sucesso em empresas brasileiras demonstram o potencial transformador dessas tecnologias, com economias substanciais e melhorias operacionais notáveis.
No entanto, a jornada para a plena adoção da manutenção preditiva e da Indústria 4.0 ainda apresenta desafios. A necessidade de investimentos em infraestrutura digital, a escassez de profissionais qualificados e as preocupações com cibersegurança são obstáculos que precisam ser superados.
Para as empresas brasileiras, o momento de agir é agora. A implementação de sistemas de manutenção preditiva não é apenas um investimento no presente, mas uma preparação essencial para o futuro. À medida que as tecnologias evoluem e novas possibilidades surgem, as empresas que se adaptarem mais rapidamente estarão melhor posicionadas para liderar seus setores.
O caminho para a Indústria 4.0 requer uma abordagem holística: investimento em tecnologia, desenvolvimento de talentos e uma cultura organizacional que abrace a inovação e a mudança contínua. As empresas que conseguirem integrar com sucesso essas dimensões não apenas otimizarão suas operações de manutenção, mas também abrirão portas para novas oportunidades de negócios e inovação.
Em última análise, a manutenção preditiva e a Indústria 4.0 oferecem muito mais do que eficiência operacional – elas representam uma mudança de paradigma na forma como concebemos e gerenciamos os processos industriais. Para o Brasil, abraçar essa revolução tecnológica é crucial não apenas para a competitividade de suas indústrias, mas também para o desenvolvimento econômico e tecnológico do país como um todo.
O futuro da manutenção industrial é preditivo, conectado e inteligente. As empresas que reconhecerem essa realidade e agirem proativamente para adotar essas tecnologias estarão construindo as bases para um futuro de sucesso na era da Indústria 4.0.